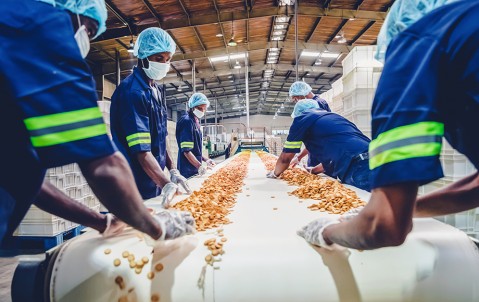
Insurers brace for spike in product recall claims
Product recall incidents have reduced during the pandemic but as lockdown is relaxed, renewed regulatory scrutiny and gaps in quality control over recent months could drive an increase in losses.
Food manufacturers have been busy. As countries went into lockdown earlier this year, supercharged consumer demand led to stripped shelves and manufacturers of staple foods like pasta and flour moving to a 24/7 operation to meet demand. It has not been the same for all food manufacturers, however, as those in the food services industry supplying restaurants and catering businesses saw demand drop overnight – and no easy way to pivot their operations to go direct to the consumer.
COVID-19 has also been a significant public health issue for food manufacturers, particularly evident in the meatpacking business, with plants in Europe and the US hit by virus outbreaks. According to the United Food and Commercial Workers International Union, 65 meatpacking employees in the US and 28 food-processing employees have died from COVID-19.
As the COVID-19 crisis took hold, food regulators were more worried about keeping the supply chain moving rather than food safety. Regulators pivoted from their prime responsibility of protecting consumers from food safety issues to not getting in the way of the supply chain and manufacturers’ key role in putting food on plates.
Despite these contrasting pandemic experiences, the incidence of product recall has been consistently low across the food manufacturing sector, even for those operations running at full throttle. Reasons for the low claims experience range from regulatory issues to less stringent quality controls, but as these factors reverse and combine with other challenges - such as plants being brought back on line after a full or partial shutdown - a claims spike over the next 18 months could occur.
As the COVID-19 crisis took hold, food regulators were more worried about keeping the supply chain moving rather than food safety. Regulators pivoted from their prime responsibility of protecting consumers from food safety issues to not getting in the way of the supply chain and manufacturers’ key role in putting food on plates. There was also the issue of having the available staff to go in and audit plants due to COVID-19 related absences and the constraints of social distancing measures.
Risk-based regulation
Risk consultancy Control Risks says government food safety inspectors have had to move to a risk-based approach in concentrating their efforts on those businesses where it is believed that the food processing activities pose a greater risk of non-compliance to food safety regulations. Food businesses with a history of compliance to Global Food Safety Initiative (GFSI) standards and consistent implementation of strong food safety management systems present a lower risk, and therefore inspections of these businesses may be suspended for the duration of the pandemic. In turn, fewer problems have been identified and fewer product recall notices issued.
Rushing to get products out will also, inevitably, have led to more mistakes during the manufacturing process, which could become a recall issue.
The shift from ‘business as usual’ also has an impact on the manufacturers themselves in terms of their own quality control. Some businesses attempting to stay on top of food safety issues, have turned to third party auditors, which conduct non-standard virtual audits. While this is somewhat effective, it is less than ideal and may not be recognised by GFSI without exploring all other options. The certification programme owner may submit a risk assessment for granting a certificate extension of up to six months to the GSFI for review. Even so, we would normally expect food manufacturers to report more errors, but the concern is the effectiveness of their quality control teams may be blunted by staff absence either through sickness or because some may have been shielding, or the company may have furloughed roles to protect its cash flow. Companies may have had to hire additional or temporary help who are not fully trained on food safety initiatives and requirements, therefore resulting in more quality or safety errors in production that could lead to adulterated products in the market.
Rushing to get products out will also, inevitably, have led to more mistakes during the manufacturing process, which could become a recall issue.
Rise in exposure
The dip in product recall, however, is likely to be only temporary as economies start to revive and exit lockdown. It is very possible the risk exposure will go up significantly over the second half of 2020 and into 2021, as regulators refocus on food safety, particularly as manufacturing plants restart. The pathogen listeria causes a high number of product recalls in the food sector. It thrives in damp conditions and the worry is that where plants have been shut down, the normal cleaning and safety procedures in place will have stopped, leading to water in parts of the plant where it hasn’t been before thanks to routine cleaning.
For manufacturers that have kept going and had to up their production, sourcing new ingredients from new suppliers might also have exposed them to food fraud - such as the intentional adulteration of ingredients or mislabelling for financial gain - given the time pressure on food manufacturers might have resulted in due diligence on new suppliers not being up to usual standards. Have the same audits been carried out for new suppliers in the supply chain that would have been carried out pre-COVID-19? Social distancing makes the job a lot harder, given the inability to send people into plants.
For manufacturers that have kept going and had to up their production, sourcing new ingredients from new suppliers might also have exposed them to food fraud - such as the intentional adulteration of ingredients or mislabelling for financial gain...
For underwriters, it means a change in the risk information requirements when looking at product recall risks. We are asking new questions such as: “If you have had to temporarily close plants, what procedures are you following to get them back up and running?” And we are looking at how robust those procedures are and any other additional steps being taken by manufacturers.
While the knock-on effects of COVID-19 will be far reaching, the crisis has revealed a flexibility in the insurance industry to reassess risk at short notice, which may become a valuable asset as food manufacturers learn to deal with the uncertainty and develop the ability to flex their business models. The recent shortage of hand sanitiser saw manufacturers with spare capacity wanting to help. We have had clients turning from drinks production, for example, to producing pure alcohol for use in hand sanitiser products. They asked whether we will cover them for product recall and we have supported them to do that, not only because the product is broadly similar but we also believed it was the right thing to do.
*****************************
This article was first published by the Insurance Day on 14th August 2020: