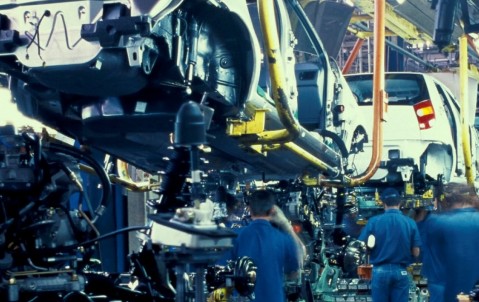
Paying the repair bill for car recalls
2014 saw a record number of cars recalled in the US. But who ends up paying the bill?
The Volkswagen emissions scandal, requiring the return of 11 million VW, Audi, Skoda and Seat vehicles to their manufacturer for repairs, is the latest mass recall in the motor industry which has seen tens of millions of cars called back by their manufacturers in recent years.
The number of cars recalled in the US reached a record in 2014. There were just over 800 recalls covering nearly 64 million cars, according to the National Highway Traffic Safety Administration (NHTSA), more than double the previous record of 31 million in 2004.
The growing number of recalls has put a spotlight on carmakers’ production methods. The “platform model” of building cars uses the same parts in more than one make or model to push down costs. But, balanced against these economies of scale is that if a fault is found in one of these parts the resulting recall is likely to be much larger, and therefore costlier.
VW has indicated that in most countries it will fix affected cars in 2016 during routine maintenance and servicing, but even such a “soft recall” involving so many vehicles is likely to be very expensive. The carmaker has put aside €6.7 billion ($7.4 billion) to repair the diesel cars with so-called defeat devices.
Who picks up the repair bill?
Although the carmaker – also known as the Original Equipment Manufacturer (OEM) – will fund and organise the recall, in reality, the final cost for many recalls will tend to be passed down the supply chain to the supplier of the faulty assembly or component.
The supply chain involved in manufacturing a vehicle is like a pyramid, with the carmaker at the top, and tiers of hundreds of smaller suppliers below it. “The supply chain is an all-important element of an OEM’s business model. But, it also means that it is heavily reliant on its suppliers. A recall of a faulty part could cause a break in this very complicated – and fragile – chain, causing havoc to an OEM’s production schedule,” says David Burke, Product Recall Line Underwriter at Hiscox London Market.
Carmakers have, over time, forged a symbiotic relationship with many of their first-tier suppliers (and these suppliers with their own subcontractors). Although it would not expect to pay for a recall prompted by a fault caused by one of its suppliers, a carmaker realises that sending the supplier at fault into bankruptcy by presenting it with a large bill could also hurt the carmaker, as the cost and time involved in sourcing new parts from an alternative supplier could far outweigh the cost of the recall itself.
What often happens is that the cost of a recall will be shared across a number of the carmaker’s suppliers. As a failure is often due to a number of factors rather than a single faulty part, so, in many cases, all of the suppliers involved in making that particular component will agree to share part of the cost.
Also, carmakers will often now contractually require their suppliers to buy product recall insurance to cover them in the event of a faulty part being inadvertently manufactured, thereby taking the financial risk out of the supply chain and passing it on to insurers.